What Makes A Good Control Panel Design?
- Ian Shaw
- Oct 19, 2023
- 3 min read
Most of us have seen a clean, well-organized control panel out on the factory floor—you know it when you see it. Conversely, it’s also easy to spot a poorly designed panel—not well laid out, crowded, messy, wires hanging all over the place, etc.
Good control panel design should feature strong layout and component placement, labelling, panel sizing and component spacing, and wireway design

The importance of control panel design cannot be understated. Industrial control panels allow you to manage the utilities and features of both hardware and software systems which comprises a range of control settings to manage the user interface, display, and more. All components need to be composed correctly and optimized to ensure the best performance. Just by taking a look at a control panel, it will be immediately obvious whether it’s been well organized or whether it can use some improvements. This will ensure that any engineer who works on it won’t have to scour through the system to find the correct motor controls, switches, relays, disconnects, or circuit protection devices. In this blog, we’re going to take a look at what comprises a good control panel.
Component Placement And Layout
With any control panel, components and component groups must be organized functionally and logically. For example, components with a high voltage rating should be placed at the top of the panel because most control panels have a main incoming power disconnect switch near the top right. As you move down the control panel, power components will have a lower voltage level.
To facilitate easy troubleshooting, power distribution components should have a breaker for the specified power level to the left, followed by distribution breakers, fuses, and terminals. This will keep things consistent, and organized, and reflect the hierarchy in schematics. Adequate space should be left between groups to allow for easier expansion if necessary.
Below the power distribution components, you should have I/O terminals and PLC racks. First and foremost, since components at the top are higher voltage, they’re putting off more heat, meaning you should keep sensitive components or heat-sensitive components near the bottom. This allows the majority of the heat to escape towards the top of the control panel. Another reason to keep these components at the bottom is due to the field instrument I/O wiring that is usually brought in towards the bottom of the control panel. This makes it much easier when I/O terminals are located at the bottom.
Labelling
Labelling is another important aspect of a good control panel design. When wiring, labels should be added to each of the wires. If there is power distribution wiring connected to a power distribution terminal, the wire should be labelled per terminal number. However, for non-PLC I/O wiring, the label is assigned according to the line number in the schematics. Wiring that connects to PLC outputs and inputs should have a label with a syntax that corresponds with the PLC address.
Power supplies, breakers, and other panel components are often labelled with abbreviated prefixes that identify the component. For example, “AC230” for 230VAC power distribution and “DI” for digital input. After that, a number is added to identify the terminal group.
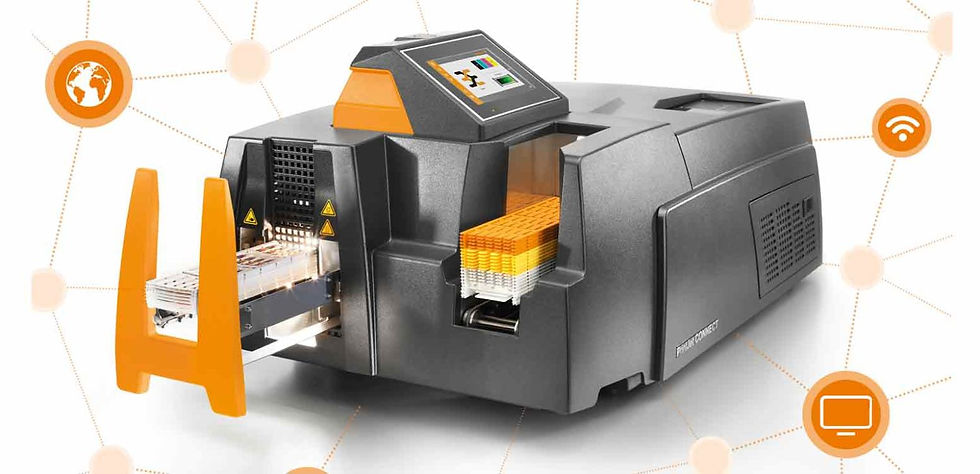
Panel Sizing
Industrial control panels are designed to allow enough space between components, both horizontally and vertically. Horizontal space will allow you to add more terminals, distribution breakers, I/O terminals, PLC racks, and more. Crowded components will also create more heat concentration which is never helpful. Vertical space can be used to organize wiring.
Wireway Design
To have a well-designed control panel, you’ll need the right amount and type of wireway. This will ensure that you have enough room for field I/O wiring and panel wiring to be routed to I/O terminals.
When the wireway is designed correctly, it will be easy to terminate internal wiring to internal panel components. Assuming you will be adding more wiring in the future, you should make sure to leave room for this when the control panel is installed.
One of the more common ways of routing cables in a panel is using Betaduct trunking
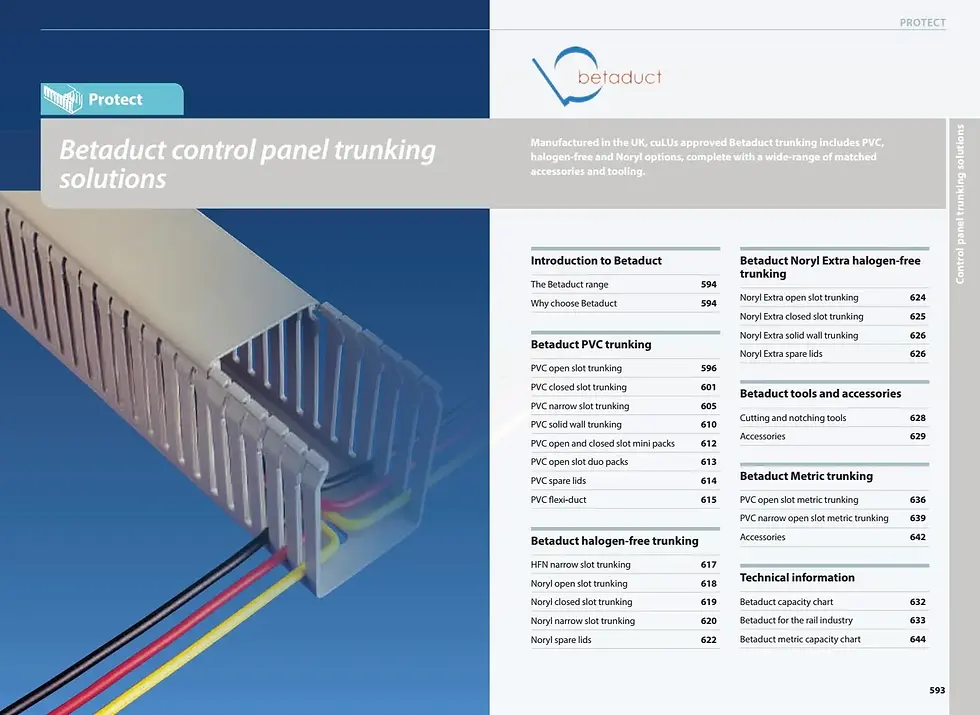
Comentários